A while back I had my ball screws and nut overhauled. I tried to rescale but it seems what ever I put in doesn’t stay. It reverts back to the factory settings. Is there an unlock function in there that will allow me to adjust it?
Also, any techniques for adjusting backlash in the controler? I can get the jog increments close but I really seem to be chasing that one. It seems that the stepper motors aren’t incrementing evenly through steps.
I basically take a cut, measure, set X offset, then use MDI to drive to a smaller diam and take another cut.
Measure and reset offset. This with the new overhauled screws gives great repeatability.
But I would really like to dial in the scaling.
Are you adjusting step count with the software or at the driver?
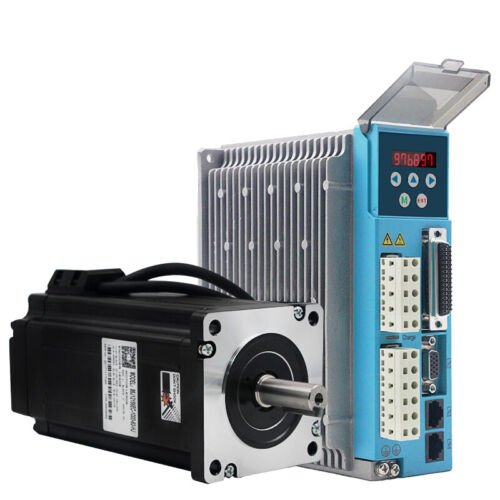
On my Mach3 mill I did not want to mess with the software stepper profile because it worked very well. I purchase 3 of these closed loop motor and driver combos. With the digital driver you can change the way the driver reacts to step and direction commands in a range from 0 to 99999. I adjusted the step count at the driver until the axis moved in perfect repeatable .001 increments. or in the case of your X axis .0005 increments to remove ,001 material from the part.
The scaling is in Admin Scale Axis I believe. It is basically a ratio of commanded to measured movement. Or visa versa. So yes in the software. I’m not sure how the backlash setting affects it either. And that is all dependent on how tight the jib is. Kind of a pain.
Actually any CNC is a pain to setup correctly. With axis mapping. Really need good equipment to do it right.
Bruce,
Where are you attempting to enter scale info? There is nothing to change on drivers for scale, except microstep dip switches which will be nowhere near the amount you want to adjust by, they’re far too coarse. Pathpilot has ADMIN commands for scale, ADMIN SET_AXIS_SCALE_FACTOR “n” “m” and ADMIN GET_AXIS_SCALE_FACTOR. The “n” you would replace with the letter of the axis to adjust and “m” with the factor amount, limited to between .995 and 1.005. Backlash setting is done with a similar command, just replace “SCALE_FACTOR” with “BACKLASH”.
Scale factor commands aren’t commonly used, it was a feature mostly developed for internal use with ballbar testing.
Yes, I was using the admin scale axis.
I would assign an axis put in a value hit enter.
Looked like it took it, no error message.
Then I would go back and admin get scaling and the valule would revert back to the original value.
And with get scaling, Z would give a not available or something similar, forget exactly.
So the company that overhauled the nuts and screws put a light grind on the screws and put oversized balls in. Like 0.0012 bigger or something.
So it all came back pretty close, but I wanted to dial it in best I could.
Backlash is pretty tricky and effects scaling I’ve been told.
Seems I’m always out a thou or so on Z.
If I do a MDI to a value in X, cut, measure, set X offset, it’s spot on.
Ideas?
Thanks
Donald, where did you purchase this combo?
Should make setting tool offsets a lot easier.
Bruce
I purchased 3 sets of driver and 8 nm closed loop stepper motors from ebay. Search leadshine closed loop stepper. You will have to weed through a lot of simpler controllers. The best price I have found is 300 dollars.
Donald, thinking about pulling the trigger on these drives. Would you send a few pics of the wiring? And maybe a description of what you did? It would be greatly appreciated.
The timing could not be worse on this request. I have just disassembled my mill to install (3 )5 to 1 hypoid gear reducers. I posted a picture of the drives in my cabinet. They are hooked directly up to 110v. The large DB connector has pins for step , direction and enabling the drive. They are hooked up directly to your breakout board. You should be able to simply unplug your drive and solder the matching wires to the matching pins. The step count per revolution are adjustable from 200 to 65535. I thought they were 99999 but I was wrong. I used the same number as the dip switch on my old non closed loop drives which was set at 4000 and adjusted them slightly from there. They are adjustable in increments of 1 which would allow you to fine tune them to match your ballscrew. I have the parameter manual for the esdh1208. it is not exactly the same but very close to the HBS1108s. The esdh2306 is the 220v version of the drive. As an aside, The stepper motor with the aftermarket 1000 count encoder has a story. The guy I bought all 3 drives from destroyed the original encoder. He thought it was the reason the drives kept shutting down. He had written a warm up program and the drives kept overheating. Servos can benefit from warm up cycles. Stepper motors are not designed to run constantly at rapid and do not benefit from warm up cycles. This ties directly into a current thread about warm up cycles on this forum. I have had no issues at all with the drives or servos. I just use them.
Wow, your in deep! Very cool.
Went to look at the drives in the lathe just to remember what the wire id was and the X drive power wires were smoked. Had some binding in X, the Gib is more of a leaf spring so it needs help. I found the standard drive on Amazon and ordered that just to get back to normal. My buddy says that steppers are at max current when they are stationary (best at holding position) but current drops as speed increases.
Ok thanks. Not there yet anyway so I’ll ping you later when maybe you have more time.
Donald, what is the pin out from the ribbon cable to the pul, dir and ena terminals? X axis on the lathe has the red stripe in that bundle. Z drive has no stripes.